Understanding HMRC's W7 Form Requirements for Duty-Suspended Alcohol Transfers in UK Bonded Warehouses
Understanding HMRC's W7 Form Requirements for Duty-Suspended Alcohol Transfers in UK Bonded Warehouses - Mandatory Filing Deadlines for W7 Forms and Documentation Requirements in UK Bonded Storage
Mandatory filing deadlines for W7 forms in the context of UK bonded storage, for duty-suspended alcohol transfers, mean you need to get these in on time to meet HMRC rules. Documentation, like proper ID showing both status and who you are, is very important. Submitting the W7 form too early or too late can mess things up badly, potentially causing problems with taxes. So, everyone involved in moving alcohol this way in UK bonded warehouses needs to understand the filing dates and what paperwork is needed. Clear knowledge here is key to avoiding problems and having smoother, less risky transactions.
The W7 form plays a key part in how the UK's HMRC handles duty-suspended alcohol transfers. Missing the deadlines for filing can trigger financial penalties and disrupt the movement of goods. It's interesting that the W7 form now has to be submitted online, requiring businesses to engage with digital tax reporting. Typically, the W7 needs to be filed before any actual physical movement of goods. This rule intends to make sure that all paperwork is done before the transport starts. Also, warehouses dealing with these duty-suspended products have to keep records, such as invoices and stock takes, for at least six years.
A late W7 submission can lead to penalties, but also might trigger an audit by HMRC which might involve a very detailed compliance check. Furthermore, the filing process requires more than just basic information; they might need extra supporting documents like proofs for claims of duty entitlement or previous records. Within bonded storage incorrect submissions cause immediate duty assessments, potential interest on dues and more costs. There can be a lot of confusion between Excise Duty and VAT; the W7 form focuses on Excise Duty specifically. Those upgrading to excise warehouses sometimes struggle with the effect of W7 rules on their new processes. Getting things right initially involves training staff and system updates. Even the slightest errors on the W7 form can cause large delays, thus implementing internal audits to catch these errors should reduce risk and enhance compliance.
Understanding HMRC's W7 Form Requirements for Duty-Suspended Alcohol Transfers in UK Bonded Warehouses - Registration Process Under WOWGR 1999 for New Warehouse Operators
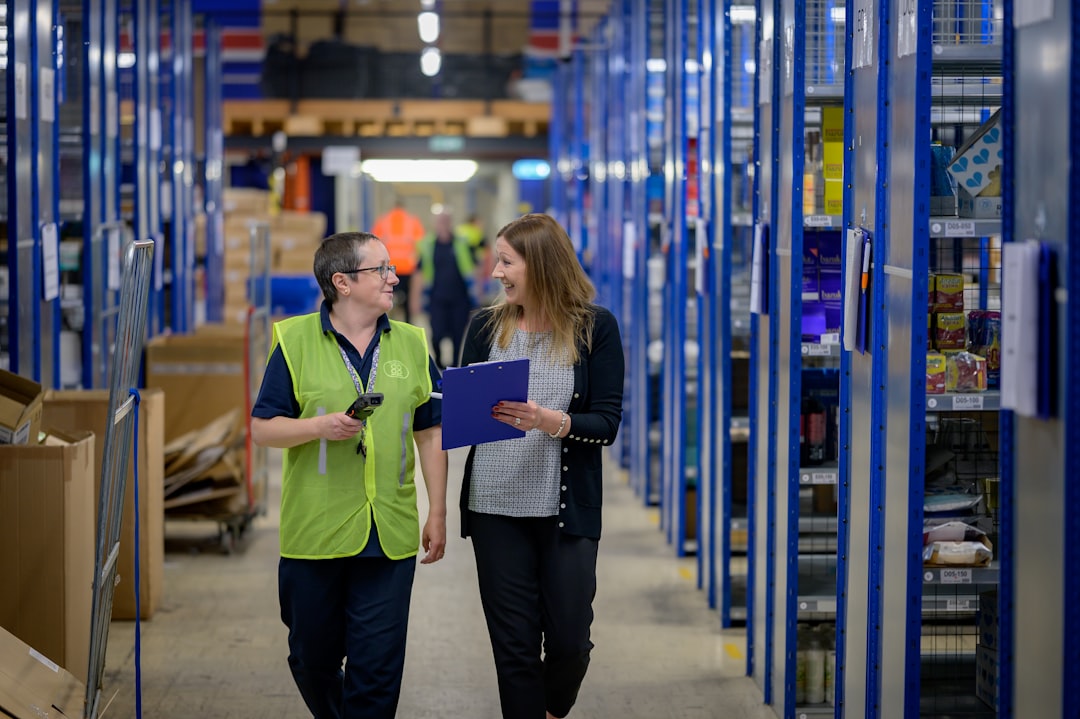
The registration process under the Warehousekeepers and Owners of Warehoused Goods Regulations (WOWGR) 1999 is essential for new warehouse operators in the UK. To legally store goods, including duty-suspended alcohol, businesses must secure approval and registration as outlined in regulation 5. This process demands not just compliance but also that warehouse operators establish themselves as revenue traders authorized by HMRC, necessitating a thorough understanding of the compliance obligations that accompany this status. For foreign companies, obtaining a GB Duty Representative certificate becomes vital in ensuring adherence to regulations. Moreover, misuse of the registration process can lead to severe consequences, such as forfeiture of goods or hefty penalties, highlighting the importance of diligence and accuracy in this critical administrative task.
The 1999 Warehousekeepers and Owners of Warehoused Goods Regulations (WOWGR) sets the stage for those looking to run a warehouse, requiring new operators to prove they’re up to the task. This involves demonstrating they’re financially solid and operationally sound. It's not just a tick-box exercise; HMRC is really looking to stop any dodgy dealings. If an operator passes muster and registers under WOWGR, they're handed a Unique Registration Number (URN). This is their ID with HMRC for all future dealings, so forgetting to include it can lead to problems. The whole registration process isn’t quick, expect it to take up to three months, and so you'd better have your paperwork all in order before you start.
Operators have to hand over detailed plans showing how they'll use the warehouse, down to the layout and security, and which needs to demonstrate that all alcohol storage rules are complied with. It seems that those who handle wines and spirits face extra scrutiny from HMRC, perhaps due to the history of fraud associated with higher priced alcohol. It's not just about the building either; everyone wanting to be involved must pass a “fit and proper test,” this looks at tax history and previous run ins with regulations. Staff training needs to be a continuous effort. Operators need to keep tabs on changes to the rules and be on top of any adjustments to enforcement - these things change and even a small shift can throw everything out of whack.
The WOWGR registration also dives into the company's financial and operational structure, asking for proof of insurance to protect against liabilities, as well as having them agree to keep super detailed transaction logs - this goes way beyond simply tracking what goes in and out. Finally, failure to comply, or not following guidelines set out by WOWGR can lead to loss of a license and risk of complete business shut down, thus forcing a full business process review.
Understanding HMRC's W7 Form Requirements for Duty-Suspended Alcohol Transfers in UK Bonded Warehouses - Movement Tracking Systems Between UK Bonded Warehouses Post Brexit
Movement tracking systems have become increasingly critical for UK bonded warehouses in the post-Brexit landscape. Businesses now face more trade complexities and regulatory hurdles. The greater need for precise tracking of duty-suspended goods emphasises the crucial role these systems play within HMRC’s requirements, especially those concerning the W7 form. As trade volume increases, customs expect super precise inventory control to avoid the errors that lead to fines. It is also important to note the difference between short-term temporary and permanent bonded warehouses and that each type requires different tracking to comply with varying storage conditions and time lines. As businesses get to grips with these regulatory changes, the effectiveness and dependability of tracking will be vital to their overall compliance and business success.
The shift after Brexit has certainly made things trickier for movement tracking in bonded warehouses. Now, extra customs checks and paperwork pile on the complexity. This has really shaken up the way logistics work, demanding a much higher standard for digital tracking. Falling short can stop operations cold until everything is in line. It's interesting that serial numbers for duty-suspended items are now super important. These tags let them follow products through the warehouse, making everyone more accountable. Some new tech, like blockchain, is being tried for tracking within these warehouses, and it looks promising in terms of giving better transparency and making supply chains smoother. It seems that fitting Internet of Things (IoT) devices into warehouses is starting to be popular - it's all about tracking goods in real-time and giving both warehouse operators and HMRC the data they need on the fly, which could mean fewer hold-ups caused by manual processes. What is also worrying is that system errors or bad data when tracking goods seems to cause real problems; not just penalties, but also supply chain hiccups that lead to more audits and cost money. The Authorized Economic Operator (AEO) status is another interesting one, as it speeds up access to customs procedures, but businesses that can’t prove they are compliant might have extended waits. The ever-changing export-import taxes make real-time data analysis a must. Modern tracking systems now use forecasting based on older data, in order to see delays before they happen. Strangely, a surprising number of warehouse operators still use very old, manual processes even though there is technology out there; this appears to be a huge compliance risk. As bonded warehouses adapt, many are linking tracking systems with broader enterprise resource planning (ERP) tools. This effort will result in an integrated system that handles compliance, inventory and reporting in a simpler manner.
Understanding HMRC's W7 Form Requirements for Duty-Suspended Alcohol Transfers in UK Bonded Warehouses - Financial Security Standards for Duty Suspended Alcohol Storage 2024
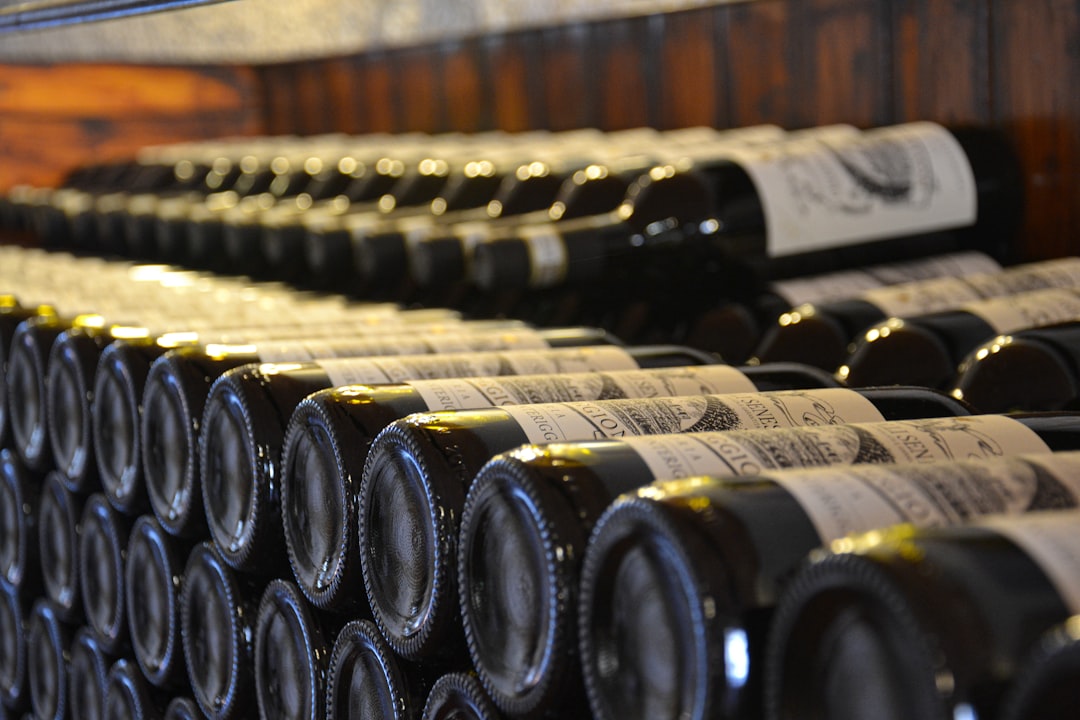
As we move into 2024, the introduction of new financial security rules for storing alcohol that’s had its duty suspended signals a big change for UK bonded warehouses. These rules mean warehouses must show they’re financially stable and handle these goods correctly, making HMRC oversight stronger. Furthermore, tweaks to Alcohol Duty rates demonstrate government action to back smaller producers, while they adapt to how things are. This affects how businesses manage these new regulations. Keeping up with these financial rules is important, not only to protect public finances, but it also forces an understanding of the most recent legal rules for transferring alcohol without paying duty. Therefore, warehouse operators must make following these new rules a top priority, so they can avoid penalties and keep operations running smoothly.
Looking deeper into the financial safeguards around duty-suspended alcohol storage in 2024, one finds a complex layer of regulations to ensure warehouses are playing it straight. HMRC are clearly keen on enforcing that every operation has the money to meet its tax obligations; they seem to now want very solid evidence, going way beyond simple bank statements to proving their financial 'backbone'. New systems need to have things like biometric security checks; presumably to keep out dodgy warehouse staff and uninvited individuals, while making sure that people are always held accountable. They also look to be moving to completely automated financial reporting systems, basically cutting out the opportunities for human mistakes, and thus reducing HMRC's pain chasing down discrepancies. They have now, finally, added a well defined schedule of penalties for infractions which is designed as a clear signal of what kind of fines can be expected for every type of transgression.
In addition, they expect warehouses to get really good insurance, that has extra coverage not just for theft, but also any potential tax debt resulting from this. All that also includes having a plan for managing really sudden increases in alcohol stock levels without letting their security, or duty reporting, fall apart. In another change, it seems that warehouses now have to prove that they invest in staff training that focusses on compliance, which might seem an odd measure, but they are relying on the idea that well-trained staff are the best protection against things going wrong. In terms of financial strategy, new rules now demand warehouses should now have specific cash reserves put aside, which can cover possible duty claims if needed, and also seems aimed at stopping warehouses from trading on their duty obligations, but it is not clear that has been an issue in the past. Furthermore, these warehouses must start using modern record keeping systems to show financial statements really fast, making sure that inventory is always lined up with the cash in the bank. Also new for 2024, is that all audits will be more transparent and this includes providing HMRC with not just the usual tax figures, but also data on their day to day operational practices, in an effort to make everything as traceable as possible and show they’re fully on top of both financial and logistics.
Understanding HMRC's W7 Form Requirements for Duty-Suspended Alcohol Transfers in UK Bonded Warehouses - Electronic Administrative Document Requirements for Cross Border Transfers
The "Electronic Administrative Document Requirements for Cross Border Transfers" dictate specific steps for businesses that move duty-suspended goods, like alcohol, using the Excise Movement Control System (EMCS). Before any goods cross a border, an electronic Administrative Document (eAD) has to be filled out and sent. This has to be done correctly, which means choosing the right "Movement Type" on the form is very important. Getting this wrong can cause problems and result in fines. It's not just about filling out forms, companies also need to let HMRC know about any changes in who owns the duty-suspended goods if they are being stored in their warehouses. This indicates a multi-layered compliance process that has to be followed by alcohol shippers.
The system for handling alcohol transfers across borders demands that you file an electronic Administrative Document (eAD) via the Excise Movement Control System (EMCS) before any movement happens. This system is really important for any international movement of excise goods, and requires that you pick the right Movement Type. Mistakes at this stage can cause problems. The eAD system needs lots of details, including specific field names and what sort of movement is being done and how it all should be done. The UK also has its own extra reporting rules for cross-border stuff that needs checking carefully. New guidelines from HMRC are out there, detailing how to submit these eADs, which they're keen you get to grips with, as all this is critical, especially after any major policy shifts. Crucially, the eAD has to be filed *before* any actual physical transfer of the goods, or you'll have legal problems. Interestingly, UK Payment Service Providers (PSPs) now have to share some details about anyone sending over EUR 1,000 into the European Economic Area. Tracking who now owns the duty-suspended goods when they get to another warehouse is your job too, as you must inform HMRC if anything changes there. Getting the eAD wrong, or late, isn’t good – expect compliance issues and possible fines. The core concept here is the EU's UCC framework which insists on electronic data exchange for cross border goods, all this intended to smooth and speed up customs for different countries. The electronic W7 isn’t just a basic requirement but is reported to have cut errors down by 30%. Moving duty-suspended goods means juggling a whole load of different documents, like the Single Administrative Document (SAD), and as of late, all are needed in electronic form to standardise the process. This electronic process helps a lot more than just compliance, it also allows real-time monitoring of the movement of goods for everyone involved, which also helps to avoid delays. Non-compliance with these rules can result in automatic audits and fines which can go as high as 50% of the unpaid revenue; this means that it's very important to get this right. Many seem to underestimate how complex the technical data is for electronic reporting; many documents require you use XML, but a lot of companies still use very old systems. Using e-docs has also promoted innovation, including the use of machine learning to pick up and predict compliance issues. HMRC now do Remote Compliance Checks to reduce physical visits, and we are expected to see more of that from 2024 onwards. It’s not only about the W7; those sending alcohol across borders now have to send safety data sheets too, to follow the environmental and safety rules, so a whole set of digital documents need to be created and maintained. Another unusual aspect is using Automatic Number Plate Recognition (ANPR) at warehouses to also track any vehicle movements that might be involved in moving duty-suspended goods.
Understanding HMRC's W7 Form Requirements for Duty-Suspended Alcohol Transfers in UK Bonded Warehouses - Audit Trail Management for Duty Suspended Stock Movements in UK Warehouses
Audit Trail Management for duty-suspended stock movements in UK warehouses has become increasingly critical due to stringent HMRC compliance measures. It’s all about keeping meticulous records to follow every step of duty-suspended goods. This makes sure everything lines up with the rules and avoids financial problems, making them far easier to handle. A solid record-keeping system is not just for avoiding fines, it is also important for streamlining HMRC inspections and audits. While new tech, such as Warehouse Management Systems (WMS) and blockchain, provide new ways of improving stock tracking and making things more compliant, it is clear that many operators still rely on old methods. This creates a major risk of not complying with the rules. To deal with the tricky rules following Brexit, warehouse owners now really need to spend money to update to current tech.
In the UK, there's a full set of rules about how duty-suspended stock must be handled, and warehouses have to keep super detailed records of every move. This means they often need advanced systems for tracking data, like product IDs, times of movement, and who was in charge.
These records have to be kept for at least six years and it's not just about ticking boxes; these can be checked thoroughly by HMRC, so, inaccurate details could mean big fines or losing a license.
Switching to digital methods for tracking stock movements has seriously cut down on mistakes. New data indicates that digital filings are around 30% more accurate than paperwork.
Some warehouses are now looking at using blockchain for stock tracking. This is an approach that could prevent data changes and offer much better transparency and tracking for duty-suspended alcohol, which helps cut risks related to fraud.
Interestingly, warehouses are now installing biometric systems, presumably to tighten security and ensure that those handling duty-suspended goods are fully accountable, therefore stopping theft and internal issues.
If a business earns Authorized Economic Operator (AEO) status they get fast-tracked customs processes as a reward. This can seriously speed up how goods are moved across borders.
What’s also interesting is that a surprising number of warehouse operators still use old-school pen and paper methods, which could leave them open to strict audits and is an obvious risk to compliance.
Since Brexit, the rules for duty-suspended stock have become tighter, forcing more paperwork on operators, who now need to be much more aware of compliance and avoiding operational problems.
For 2024, warehouses now need to show they're financially solid, and not just by showing a tax statement. They have to also now have proper plans for how they will handle unexpected increases in inventory that might mess up duty reports.
Advanced tracking software that analyses real-time data is now needed to try and flag potential problems *before* they happen. The system tries to use historical data to try and predict what might go wrong, allowing for smoother tracking and audits.
More Posts from tradeclear.tech: