Transforming Warehouses with AI for Better Trade Compliance
Transforming Warehouses with AI for Better Trade Compliance - Connecting warehouse data streams to trade compliance platforms
Connecting the detailed operational data flowing from warehouse floors directly into trade compliance systems is proving fundamental in navigating the increasingly complex global trade landscape as of mid-2025. This integration, frequently enhanced by advancements in artificial intelligence, aims to transform raw data streams into actionable insights. The goal is to move beyond static reporting, enabling professionals to gain a clearer picture of shipment specifics and potential risks in near real-time. While the vision promises improved visibility, more efficient workflows, and the ability to anticipate compliance hurdles proactively, a persistent challenge lies in harmonizing disparate warehouse management systems and logistics data sources. Ensuring the accuracy and reliability of these combined data streams is a critical prerequisite that is often more difficult in practice than in concept, yet it remains essential for effective compliance in dynamic global markets.
Shifting focus from simply tracking inventory, warehouse systems are now finding unexpected utility in trade compliance by correlating granular sensor data, like precise weight and dimensions collected primarily for logistics efficiency, with product master data. This provides a more objective, physical basis for initial automated tariff classification suggestions, although the accuracy still hinges on sensor calibration and the fidelity of product data linkages.
The notion of "real-time" compliance enforcement within the warehouse becomes tangible, if technically challenging. As global restrictions update, ideally the integrated system could immediately trigger holds on specific items or even entire shipments physically residing in the facility, pre-departure. The critical questions remain around system latency, resilience, and the reliability of propagating complex policy changes into actionable, automated warehouse tasks.
Peeling back the layers, analyzing the complex spatial and temporal sequences of item movements inside the warehouse goes beyond simple quantity checks. It offers a data-rich canvas to identify potential compliance vulnerabilities, perhaps revealing patterns indicative of unauthorized commingling, suspicious deviations from standard process flows, or unusual dwell times that might signal deeper issues traditional audits could easily miss.
Leveraging warehouse operational timestamps and item sequencing data, predictive models are being applied to flag shipments exhibiting statistical characteristics historically associated with increased customs scrutiny or a higher likelihood of requiring additional documentation. While aiming to preempt delays, the effectiveness and potential for false positives or biases in these algorithms, trained on historical data that may not reflect future conditions, warrant careful consideration.
Finally, the aspiration is a closed-loop feedback system. Should a compliance platform identify an issue with a shipment's data post-warehouse processing, the feedback loop could theoretically trigger automated corrective actions or re-verification steps directly within the warehouse workflow for subsequent, ostensibly similar items. This requires robust data pipelines and sophisticated workflow automation that can dynamically adapt processes without constant manual oversight, presenting both a technical leap and a governance challenge.
Transforming Warehouses with AI for Better Trade Compliance - Performing compliance validation during warehouse operations
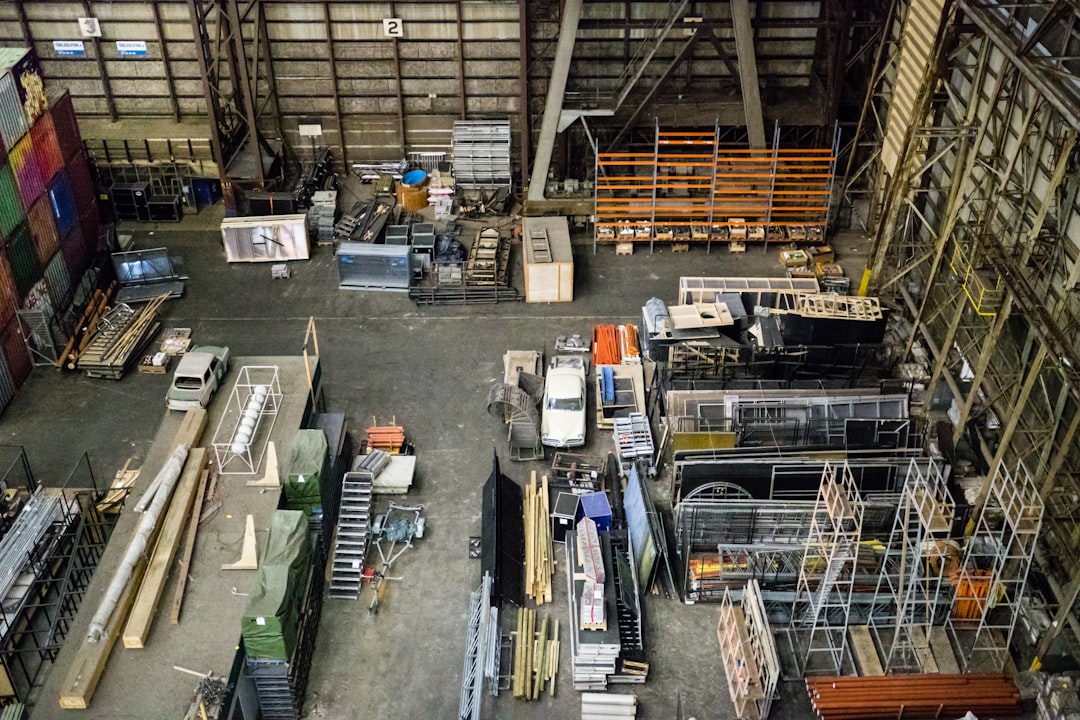
Performing compliance validation directly within warehouse operations is becoming a more pronounced focus as global trade complexity grows. The adoption of artificial intelligence tools holds promise here, enabling automated checkpoints designed to verify that warehouse activities, from receiving to picking and packing, adhere to the necessary trade regulations and standards. This proactive verification approach isn't merely about avoiding fines; it also has the potential to improve the fluidity of warehouse tasks by identifying potential compliance snags before goods even leave the facility, theoretically leading to smoother processing and reduced delays.
However, depending on automated validation mechanisms within the dynamic warehouse environment is not without its complexities. A significant challenge lies in ensuring the reliability of the validation outputs – the possibility of the system incorrectly flagging compliant actions as problematic (generating false positives) is a genuine operational concern that could lead to unnecessary disruptions. Moreover, effectively performing these automated checks relies heavily on the quality and consistency of the data being fed into the systems, a challenge amplified by the often fragmented nature of data sources across different warehouse technologies. For compliance validation during operations to be truly impactful, addressing these data integrity issues and refining the accuracy of automated checks are critical steps needed to build trust in the process.
Examining the practicalities of validating trade compliance *during* the actual flow of goods within a warehouse environment reveals some counter-intuitive constraints. For instance, obtaining highly precise, item-level spatial and temporal tracking data, seemingly a digital problem, is profoundly impacted by the physical environment itself. The very structures and packaging materials surrounding items can interfere with positioning signals, introducing ambiguity that algorithms then struggle to reconcile with expected process flows. Further complicating matters, subtle environmental shifts – a change in humidity altering carton weight, or temperature affecting material density – can introduce small but significant variances in physical measurements, challenging the consistency checks automated validation systems rely on for detecting anomalies.
From a computational perspective, establishing statistically sound validation against rare but high-impact non-compliance events necessitates correlating vast quantities of diverse data streams. This isn't merely a large data problem; the computational density required can scale towards analyzing petabytes daily just to spot faint signals of deviation amidst the noise of standard operations, demanding infrastructure with formidable processing capabilities and, consequently, substantial energy requirements.
It's also intriguing to observe how the physical constraints imposed by the warehouse layout and the specific material handling equipment in use inherently influence the *types* and *likelihoods* of process deviations that might occur. This physical reality introduces a form of bias into the operational data, which any validation algorithm must implicitly or explicitly account for if it hopes to accurately flag deviations rather than simply reflecting the facility's physical limitations. The sheer scale and speed of data generated by dynamic warehouse operations – every scan, every move, every measurement occurring in near real-time – doesn't just create a data pipeline challenge; maintaining the necessary processing and storage infrastructure to keep pace presents a significant energy demand, a thermodynamic reality often overlooked in discussions of digital transformation.
Transforming Warehouses with AI for Better Trade Compliance - Responding to regulatory changes via adaptable warehouse AI systems
Given the fluid nature of trade rules as of mid-2025, flexible AI tools within warehousing are becoming crucial for responding effectively to updates. These AI-driven systems support keeping pace with shifts, enabling facilities to grasp new requirements and modify operations reasonably quickly, aiming to lessen the potential for oversight. Leveraging sophisticated analytics, operations can attempt to foresee upcoming rule changes and proactively adjust processes, shifting from purely reactive postures. However, deploying such systems presents real hurdles; ensuring the quality and dependability of incoming data streams remains paramount to preventing costly errors and operational disruptions. Overall, embedding flexible AI within warehouse workflows signifies a notable step toward constructing a more agile, transparent, and effective compliance framework in an increasingly complicated global trade landscape.
Even with rapid cloud infrastructure provisioning available by mid-2025, the practical task of fully retraining and validating complex AI models to accurately reflect the nuances of a significant new trade regulation across potentially millions of product variants can still span several days, creating an unavoidable lag before automated processes are truly aligned.
A single, seemingly straightforward amendment to international trade rules can cascade into the need for modifications across thousands of interconnected logic rules and decision trees within a warehouse AI system's configuration, leading to a combinatorial explosion in the necessary testing scenarios to prevent unintended compliance failures with other, unaffected regulations.
High-fidelity digital twin simulations of warehouse operations, originally developed for throughput optimization and layout analysis, are proving unexpectedly critical for researchers needing to safely stress-test how adaptable AI systems *might* behave under hypothetical future regulatory landscapes or disruptive updates before deploying changes to live operations.
Translating abstract or principles-based language common in new regulations into concrete, executable rules that a warehouse AI system can reliably act upon frequently requires extensive, often protracted, human-in-the-loop feedback cycles; AI models still exhibit difficulty autonomously grasping the *intent* behind regulatory text without significant, specific examples and corrections from domain experts.
Counter-intuitively, a continuous stream of frequent, minor regulatory tweaks can pose a greater adaptation challenge for warehouse AI systems than a single, large overhaul, primarily due to the cumulative overhead of constant model redeployment and the heightened risk of introducing conflicting or subtly inconsistent rule interpretations across successive system updates.
Transforming Warehouses with AI for Better Trade Compliance - Applying AI within warehouses to reduce compliance errors and costs
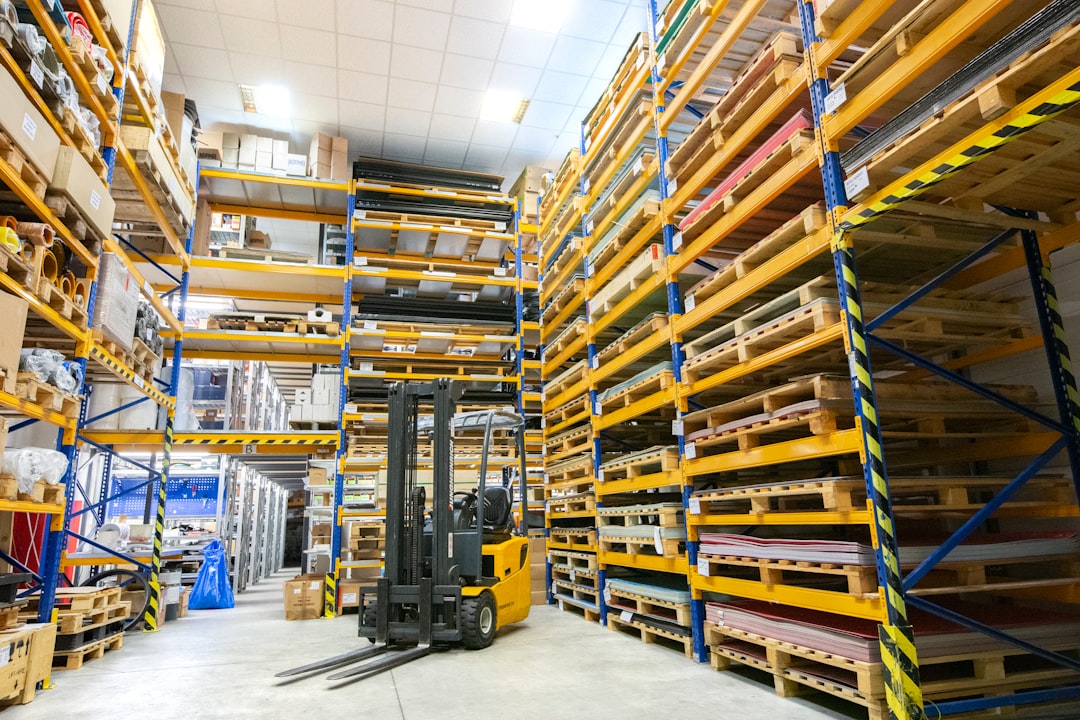
Warehouses are increasingly leveraging artificial intelligence, partly to tackle the challenge of trade compliance errors and their associated expenses. The focus is often on using AI to automate checks directly within day-to-day operations, such as when goods arrive, are picked, or are packed. The idea is that by embedding these automated validation points, facilities can better ensure adherence to diverse trade regulations, thereby mitigating the risk of fines and processing delays. However, placing significant trust in these automated compliance checks isn't straightforward. The consistency and reliability of the system outputs are a genuine concern; systems can sometimes incorrectly flag perfectly compliant actions, creating unnecessary hold-ups. Furthermore, the practical challenges posed by the physical environment itself, coupled with the perpetual need for high-quality data input, present ongoing hurdles that can complicate the effectiveness of AI in truly eliminating compliance slip-ups within the warehouse setting.
Examining the practical applications of artificial intelligence within warehouse environments to specifically address trade compliance issues reveals several dynamics that warrant closer inspection as of mid-2025:
Contrary to focusing solely on data analytics, some AI implementations are pushing into the physical realm. Systems are now designed to interpret compliance risk scores for individual items or pallets and, rather than just generating alerts, automatically deploy autonomous mobile robots (AMRs) or automated inspection equipment to perform targeted, on-the-spot visual inspections, weigh checks, or RFID scans on that flagged cargo right on the warehouse floor before it moves forward.
Developing effective AI models for trade compliance unearths a peculiar data challenge that isn't simply about volume. While warehouse operations generate floods of data, the *specific* data points relevant to highly niche regulations or procedures only applicable to rare goods or infrequent trade lanes are often extremely sparse. This presents a significant hurdle for traditional machine learning, requiring advanced statistical techniques to learn robust patterns from a mere handful of historical examples.
While AI demonstrably excels at automating repetitive checks and mitigating common human errors like misreading labels or manual data entry mistakes, its inherent nature introduces a different kind of potential failure mode. Errors in AI-driven compliance processes are less likely to be random, isolated incidents and more likely to be systemic, stemming from subtle biases baked into the training data or fundamental misinterpretations of complex or context-dependent rules during the model's development.
Early behavioral observations from facilities deploying pervasive AI monitoring suggest complex and sometimes counter-intuitive effects on human operator behavior. The constant awareness of automated oversight designed to enforce compliance can potentially reduce overt rule-breaking, but it might also subtly alter workflow patterns, perhaps leading operators to develop novel, unexpected ways to complete tasks that skirt the edges of automated checks, effectively attempting to navigate or 'solve' the AI system itself.
Although the computational demands for training and running sophisticated AI compliance models can be substantial, leading to significant energy consumption at the data center level, the operational efficiencies gained by minimizing compliance errors – reducing costly re-sorting, avoiding incorrect shipments that require reverse logistics, and optimizing process flows to prevent deviations in the first place – can, in certain configurations, surprisingly lead to a *net* reduction in the overall energy footprint associated with compliance-related activities within the facility.
Transforming Warehouses with AI for Better Trade Compliance - Ensuring data integrity at the source for accurate trade declarations
Establishing the trustworthiness of data right where it originates is paramount for crafting accurate trade declarations amidst the complex currents of global commerce. As warehouse operations increasingly adopt advanced technologies, particularly those incorporating artificial intelligence, ensuring the fundamental reliability of the incoming data streams becomes critically important. Any inaccuracies or inconsistencies at this foundational level can propagate through the entire process, potentially leading to costly compliance failures and operational disruptions. Effective data oversight must therefore extend beyond simply collecting information; it requires rigorous validation mechanisms applied as early as possible within the warehouse workflow. Furthermore, in an environment of constantly shifting trade regulations, the capacity to reliably track data back to its source and confirm its initial accuracy is essential for adapting operational procedures and maintaining adherence. Fundamentally, without this solid bedrock of data integrity at the point of origin, even the most sophisticated AI systems designed to support compliance are inherently built on shaky ground and risk producing unreliable outcomes, underscoring the continuous need to scrutinize and improve how data is handled from the outset.
Examining the challenge of ensuring data integrity right at the point where it's first captured within the warehouse environment reveals some often overlooked complexities.
It's observed that even minute, cumulative wear on physical sensors used for capture – whether optical scanners, load cells, or dimensional measurement systems – doesn't just lead to simple, uniform offset errors. Instead, the resulting data inconsistencies can be highly specific to the interaction geometry or the environmental micro-state at the instant of measurement, making blanket correction difficult.
The very material composition and structure of packaging often dictates how reliably identification signals, particularly those relying on radio waves or light interaction like RFID or barcode scanning, can be captured at the source. Subtle differences in density, coatings, or internal bracing can unpredictably absorb, reflect, or scatter signals, complicating the process of obtaining a consistent and reliable primary key linking a physical item to its digital record.
In scenarios still requiring human interaction for data capture – even seemingly straightforward tasks like accurately positioning an item for an automated scan or scale reading – the inherent variability in human motor control and subtle differences in technique between operators introduce statistical noise into the 'source' data points. This variability isn't easily predictable or linearly correctable across a diverse workforce.
Regardless of digital sophistication, the fundamental physical principles governing data acquisition – such as the signal-to-noise ratio dictated by ambient light levels, acoustic interference, or localized electromagnetic fields at the exact capture location – impose a non-negotiable, real-world constraint on the ultimate integrity achievable at the initial point of observation before any processing occurs.
Ensuring robust data integrity at the source isn't solely about the recorded value itself, but critically about the *context* of its capture. The precise temporal synchronization of readings from multiple disparate sensors involved in a single event (e.g., scanning, weighing, imaging simultaneously) often reveals subtle misalignments or latency issues, complicating efforts to construct a perfectly consistent, irrefutable record of the physical state at that exact moment from potentially asynchronous inputs.
More Posts from tradeclear.tech: